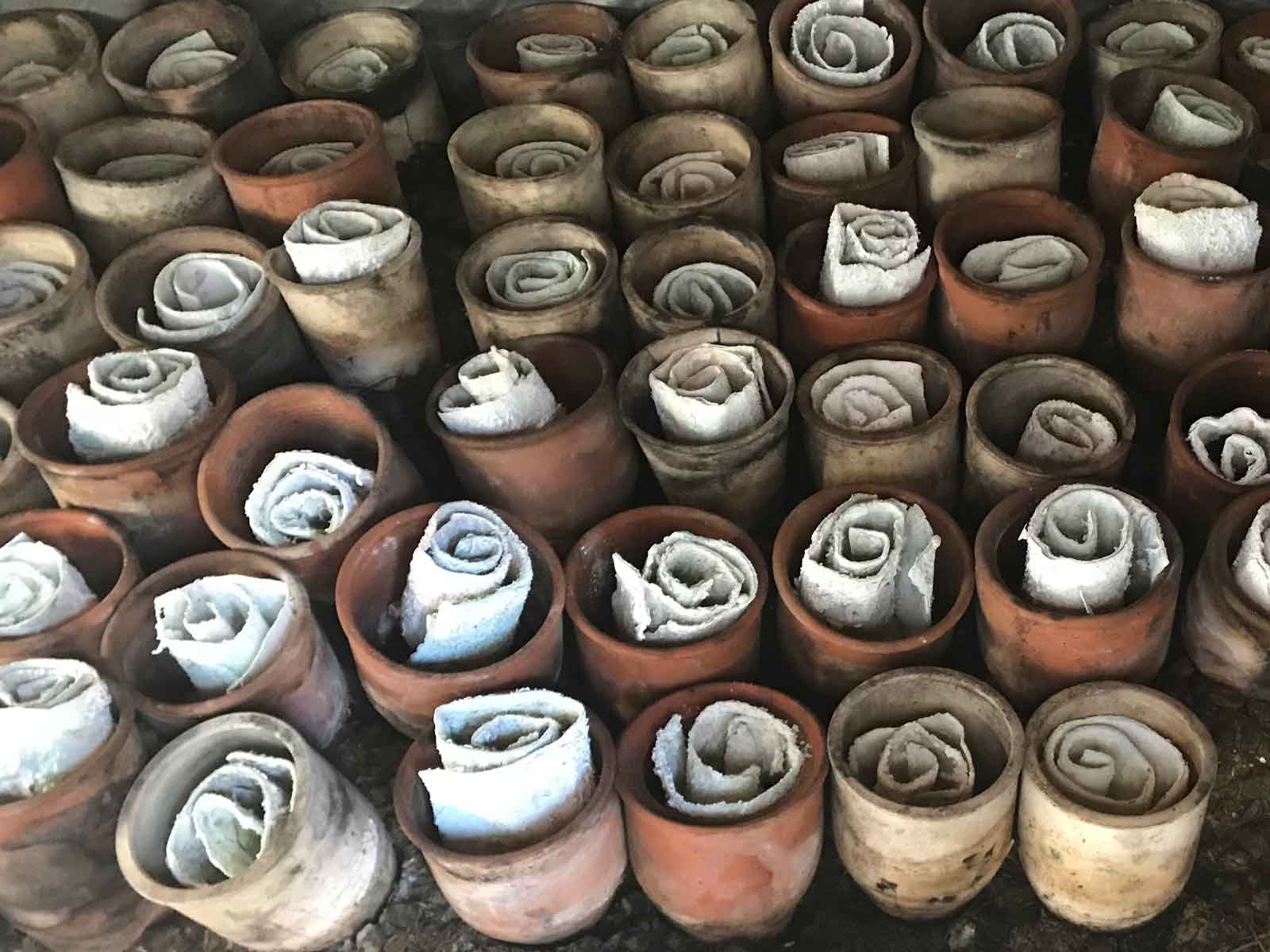
Making stack process flake white (or lead white made according to the “old Dutch method”) is time-consuming and prone to variations in the resulting pigment. These variations are not surprising and were well-known among manufacturers of lead white based on literature and historical documents of the process. It was a significant issue of the process that manufacturers dealt with in various ways.
In his article on lead white, Edward Brown describes the stack process with remarkable detail:
Lead buckles are packed in porcelain or earthenware pots known as “corroding pots,” having at the bottom a well filled with dilute acetic acid or vinegar. When filled, they are placed in stacks, tier on tier, surrounded by tanbark, with proper provision for admission of air and escape of moisture and gases. After ninety to a hundred and twenty days, the corrosive action is complete, and the stacks are taken down. The corrosive action is very peculiar. Briefly, the process consists of the volatilization of acetic acid by the heat generated in the fermentation of the tanbark. The acetic acid thus liberated attacks the lead at the surface of the buckles forming basic lead acetate. The carbonic acid also generated by the tanbark, in turn unites with the acetate, setting free neutral lead acetate to attack fresh layers of the lead: the layer first attacked being converted into basic lead carbonate or lead hydrocarbonate. This process continues progressively through the buckle. By selection, the corrosions are so graded as to give a practically uniform product. The more carbonate the product contains, the whiter the lead. The more hydroxide it contains, the better it will work under the brush. The old Dutch process lead is a sort of compromise between the carbonate and the hydroxide. The corroded buckles are run into separating cylinders, then ground to separate the remaining particles of lead. The ground lead is next washed and passed on into settling tanks. Finally, it is pumped into steam-jacketed copper pans to dry.
“It will be evident,” says Terry, a well-known English authority, in his book, Pigments, Paint and Painting, “that the mode of proceeding in white-lead making by the stack process is most crude and clumsy, and a most uncertain method, one governed by rule-of-thumb, and by no element of certainty or science. . . . The uncertainty of the stack process is shown most clearly in this: that stacks may work, and some do not work. In the latter case, all the time and labor spent in forming the stacks and all the acid they contained is lost. No amount of foresight will avail to determine beforehand, which stack shall accomplish the conversion of the contained metallic lead, and which will not.”
Although the incrustation that is most esteemed by the manufacturers is “a hard, china-like material, formed of thin deposits, layer upon layer, in a slow, continuous, regular way,” it is impossible to foresee whether this kind of white-lead will result from any given corrosion, because it is almost impossible to subject all portions of the stack to the same conditions or the same action of the corroding gases. (Brown 51)
The author of The Lead and Zinc Pigments, notes that the process yielded unpredictable results:
“...with a process which admittedly does not give a uniform product at all times, it is easy to see how quality may at times be sacrificed for quantity. It was formerly the custom of the most careful corroders to sort and separate out the imperfect corrosions, and in addition age their lead by storing in large bins for a considerable length of time before grinding in oil, and the writer understands that this custom still prevails among the conservative English manufacturers to-day.” (Holly 66)
When Natural Pigments makes lead white according to the stack process, or the old Dutch method, we encounter the same issues as manufacturers of previous centuries. We obtain variations in pigment particle size and chemical composition. This results in a visibly different appearance and behavior, most of which are useful in artists’ paint. We record variations in each batch and note that, for the most part, we achieve uniformity by carefully selecting batches and holding out a product that exceeds typical specifications. From time to time, however, we obtain pigment where the entire batch is outside our typical specifications yet may yield an exciting and functional paint.
This occurred with a lot of what we call the “Winter 2018 Batch,” or batch 4093. The batch had an enormous particle size and hardness. Despite these variations, we decided to produce oil paint from this batch. The unusual properties of stack process lead white are revealed in works of the old masters, such as those of Rembrandt, and is why we see unusual brush handling not possible with modern lead white pigment.
Ernst van de Wetering describes these effects in Rembrandt: The Painter Thinking:
One of the most surprising discoveries concerned the working properties of lead white pigment prepared according to the Old Dutch method. This pigment differs radically from present-day lead white in the conspicuous variation in the size of its granules, in contrast to the regular granule size of modern preparations. The specific ease of working of seventeenth-century lead white explains a great deal about Rembrandt’s surface textures in the lighter passages: the paint flows easily, but at the same time, it often remains ‘standing’ just as it left bristles of a brush.
To better understand how batch 4093 differs from our typical batch of stack process flake white, we describe some of the tests we use to quantitatively measure each portion of each bath we produce of stack process flake white.
Particle Size Measurements
A Hegman gauge sometimes called a grind gauge or grindometer, is a device used to determine how finely ground the particles of pigment dispersed in a paint sample. The gauge consists of a steel block with a series of tiny parallel grooves machined into it. The grooves decrease in depth from one end of the block to the other, according to a scale stamped next to them. A Hegman gauge is used by puddling a sample of paint at the deep end of the gauge and drawing the paint down with a flat edge along the grooves. The paint fills the grooves and the location where regular, significant “striations” in the appearance of the paint mark the coarsest-ground dispersed particles. The reading is taken from the scale marked next to the grooves in dimensionless “Hegman units” and mils or microns.
The Hegman units for most of our batches, such as batch 3589, are 5.5, whereas, for batch 4093, it is 0. This means that the largest particles in our standard batches are about 30 microns, wherein batch 4093 particles as large as 101 microns are present. However, it should be noted that the Hegman units represent the largest particles in a paint sample and that many particles are less than this size. To provide a visual concept of particle size in microns, very fine sand is around 100 microns, and the average width of human hair is about 50 microns.
Although batch 4093 contains coarse particles, most are less than 100 microns. It brushes out with a noticeably visible grain that can be seen in the image above and in the drawdown (pictured below).
How We Measure Color and Opacity
To compare color and opacity from batch to batch, we apply samples of a standard batch onto a card alongside the batch we are comparing. A small amount of paint from each sample is placed at the top of an opacity chart, a specially prepared card with a lacquer coating. The paint is “squeegeed” with a blade applicator from the top and drawn down the card towards the bottom at a uniform thickness and spreading rate.
The blade applicator provides an accurate and reproducible method of applying paint to a flat surface. Since most physical properties of paint depend on thickness, it is essential that the thickness of a coating must be reproducible, and the correct thickness must be known. Applicator blades make this possible by setting the clearance between the bottom of the blade and the flat surface at a precise distance and then applying wet paint, which is just one-half of that clearance.
In the chart above, we set the applicator blade to 6 microns and spread the paint at a uniform thickness of 3 microns (pictured above). Batch #4093 appears to have the same opacity as the standard batch (in this case, we compared it to batch #3598). The color is noticeably darker, appearing as a light buff compared to the card’s brilliant white background. There is also a visible grain or texture in the paint.
The differences in color and particle size may result in interesting behavior for the artist. We release this batch (and perhaps future ones) to provide artists with a greater variety of paints than those commercially available.
Where to Buy
Resources
For more information on how Natural Pigments makes stack process flake white, how it was made throughout history, and how it differs from modern lead white, please read Stack Process White Lead: Historical Method of Manufacture. Another article, Notes About Stack Process Lead White, discusses differences between modern lead white and our production of stack process flake white pigment.
Confused about the difference between flake white and Cremnitz white? The article, Flake White and Cremnitz White, explains the origins of these names and resolves the confusion.
Please read the article What Whites are Best for Your Oil Painting? for a complete description of white pigments used in artists' paints.
References
Clifford Dyer Holley, The Lead and Zinc Pigments, Wiley, 1909.
Edward Hurst Brown, "White-Lead: Its Advantages and Its Faults." The American Architect and Building News, Volume 64, Boston: James R. Osgood & Company, 1899.
Ernst van de Wetering, Rembrandt: The Painter Thinking, Berkeley, California: University of California Press, 2016, ISBN 0520290259, 9780520290259.
George Terry, Pigments, Paint and Painting, Reprint by CreateSpace Independent Publishing Platform, 2018, ISBN 1987672100, 9781987672107.