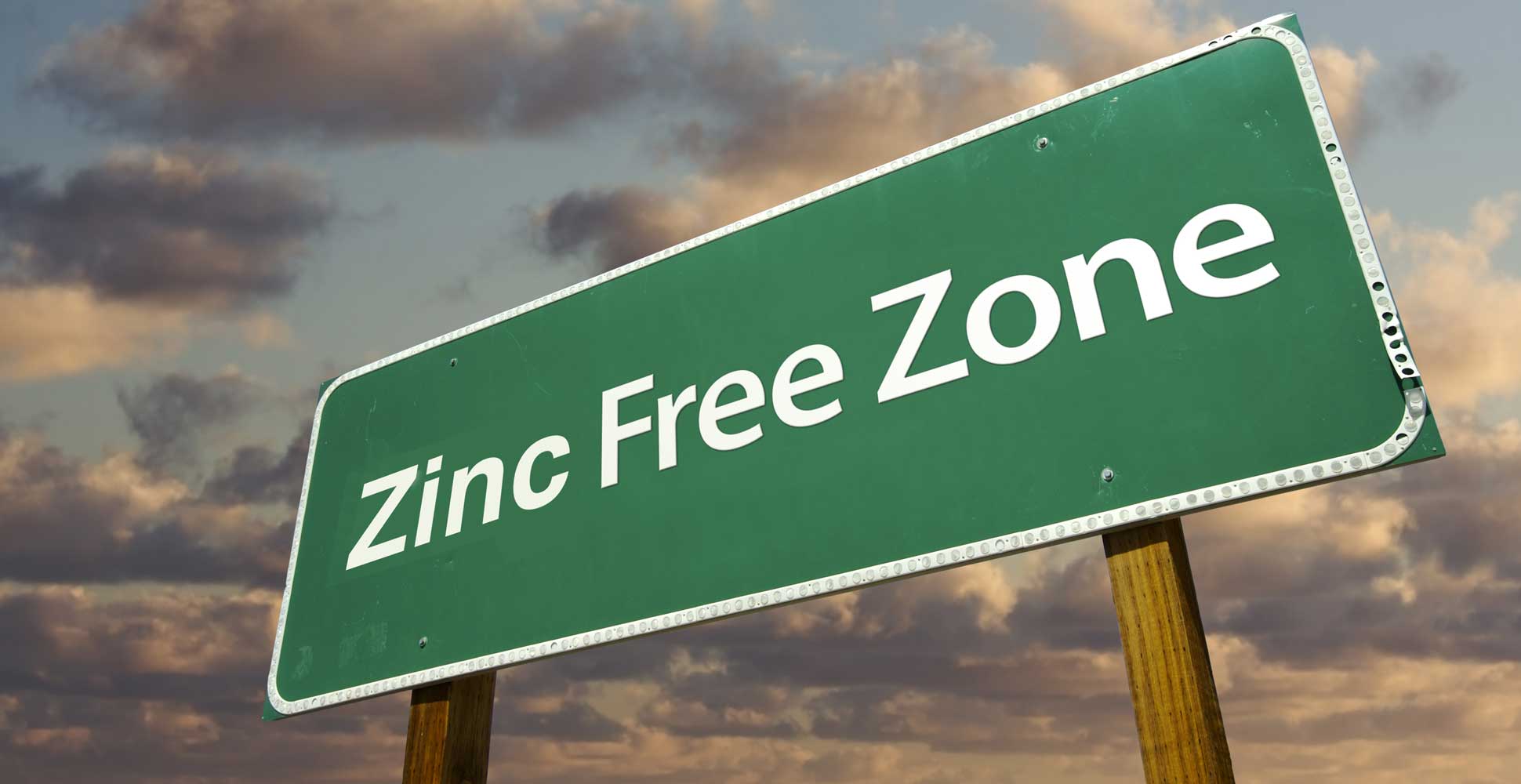
A paper by scientists at the Smithsonian’s Museum Conservation Institute exposes long-term problems with zinc white in oil paint. The report “The Chemical and Mechanical Effects of Pigments on Drying Oils” describes the highlights of a 28-year study on the stability and strength of oil paint films. The results reveal important implications for artwork made with artists’ oil paints containing zinc white.
A 28-year study exposes the potential problems of zinc oxide in artists’ oil paint.
The paper by Marion Mecklenburg and Charles Tumosa examines the drying of different drying oils, traditional pigments, and commercially prepared artists’ oil paints. It also studies the differences in the effects of pigments on paints' long-term stiffening and film formation. For the study, different pigments were ground in different oils, applied to polyester films, and stored in a controlled environment. Over the years, the paints were removed from the polyester film and tested mechanically as unsupported thin films.
Fig. 1 Detail of a painting by Henry Cliffe, painted in 1959, shows severe cracking and interlayer cleavage in paint containing lead white and zinc white.
Zinc White Causes Oil Paint to Become Brittle
Among the results, several white pigments were studied, including lead white (basic lead carbonate), titanium white (titanium dioxide), and zinc white (zinc oxide). What is of interest about the paints made with zinc oxide and drying oils is that they become incredibly brittle in as little as three years. The report shows that a 14.5-year-old paint snaps like glass when bent. It compares a 14-year-old paint made with lead white and linseed oil, which can elongate 4.5% before breaking, to zinc white paint of the same age, which can only elongate 0.3%.[1]
Another startling fact revealed by the report about paints made with zinc white—they peel off. Paint layers containing zinc white delaminate. The photograph of a painting by Henry Cliffe (Fig. 1) shows this damage resulting from rolling the painting.[2]
The delamination is not limited to layers of oil paint. The paper describes the test of many commercial acrylic emulsion grounds upon which commercial and custom-manufactured oil and alkyd paints were applied. The commercial lead white and titanium white oil paints containing zinc white became brittle after seven years of drying, and the paints with zinc white were delaminated (Fig. 2). Paints containing zinc white were easily and cleanly separated from acrylic emulsion grounds.[3]
Fig. 2 Commercial acrylic ground underneath a layer of commercial lead white oil paint containing zinc oxide. The paint could be peeled away from the acrylic ground with little effort.
The brittle paint film and delamination observed in the tests by Mecklenburg and Tumosa are not confined to zinc white alone in oil. The paper’s authors tested zinc oxide combined with other white pigments, such as lead white and titanium white.[4]
Should Artists Using White Oil Paint Be Concerned?
The study's results highlight a major concern for artists today. The majority of white oil paint available today includes zinc white. This may point to the early failure of many artworks in the future. Table 1 lists the pigments and drying oils included in commercial oil paint when the manufacturer identified these components on the label. (Manufacturers complying with ASTM D 4302 Standard Specification for Artists’ Oil, Resin-Oil, and Alkyd Paints list the pigments on the label. The common name and Colour Index designation are used to identify the pigments.[5] Not all artists’ materials manufacturers comply with this standard.) For manufacturers complying with the standard, the table reveals that many white colors contain zinc white. The table does not reveal the zinc that may be included in white oil colors by manufacturers not conforming to the standard. ASTM does not enforce its voluntary standards. Some companies may copy ASTM terminology on their labeling and in their literature without actually conforming with ASTM D 4302.
Table 1 Commercial Artists’ White Oil Paint
This is the original table published in 2007, with additions in 2014. For an updated table of the current pigments of commercial oil colors, please see Appendix A.
Brand Names White Oil Color |
Pigment Common Names and Colour Index Names* |
Vehicle (Drying Oil) |
Art Spectrum Artists’ Oil Colors | ||
Titanium White | Titanium dioxide (PW 6), zinc oxide (PW 4) | Safflower oil |
Titanium White No. 2 | Titanium dioxide (PW 6), zinc oxide (PW 4) | Safflower oil |
Zinc White | Zinc oxide (PW 4) | Safflower oil |
Blockx Artists’ Oil Colors | ||
Flake White | Lead white (PW 1) | Poppyseed oil |
Mixed White | Lead white (PW 1), zinc oxide (PW 4) | Poppyseed oil |
Titanium White | Titanium dioxide (PW 6) | Poppyseed oil |
Titanium-Zinc White | Titanium dioxide (PW 6), zinc oxide (PW 4) | Poppyseed oil |
Zinc White | Zinc oxide (PW 4) | Poppyseed oil |
Daler-Rowney Artists’ Oil Colour for Artists | ||
Flake White | Lead white (PW 1), zinc oxide (PW 4) | Safflower oil |
Titanium White | Titanium dioxide (PW 6) | Safflower oil |
Zinc White | Zinc oxide (PW 4) | Safflower oil |
Daniel Smith Artists’ Oil Colors | ||
Titanium White | Titanium dioxide (PW 6) | Safflower oil |
Zinc White | Zinc oxide (PW 4) | Safflower oil |
Da Vinci Paint Co. First Quality Artists’ Oil Colors | ||
Titanium White | Titanium dioxide (PW 6) | Safflower oil |
Zinc White | Zinc oxide (PW 4) | Safflower oil |
Gamblin Artists’ Oil Colors | ||
FastMatte Titanium White | Titanium dioxide (PW 6), zinc oxide (PW 4) | Linseed oil and alkyd resin |
Flake White Replacement | Titanium dioxide (PW 6), zinc oxide (PW 4) | Alkali-refined linseed oil |
Quick Dry White | Titanium dioxide (PW 6) | Oil-modified alkyd resin |
Radiant White | Titanium dioxide (PW 6) | Poppyseed oil |
Titanium White | Titanium dioxide (PW 6), zinc oxide (PW 4)** | Alkali-refined linseed oil |
Titanium-Zinc White | Titanium dioxide (PW 6), zinc oxide (PW 4) | Alkali-refined linseed oil |
Zinc White | Zinc oxide (PW 4) | Alkali-refined linseed oil |
M. Graham & Co. Artists’ Oil Colors | ||
Titanium White | Titanium dioxide (PW 6), zinc oxide (PW 4) | Walnut oil |
Grumbacher Pre-Tested Artists’ Oil Colors | ||
Flake White | Lead white (PW 1), zinc oxide (PW 4) | Alkali-refined linseed oil |
MG® Underpainting White | Titanium dioxide (PW 6), zinc oxide (PW 4) | Oil-modified alkyd resin |
Suberba™ (Titanium) White | Titanium dioxide (PW 6), zinc oxide (PW 4) | Walnut and poppy oils |
Titanium White (original formula) | Titanium dioxide (PW 6), zinc oxide (PW 4) | |
Titanium White (soft formula) | Titanium dioxide (PW 6), zinc oxide (PW 4) | Poppyseed and sunflower oils |
Zinc White | Zinc oxide (PW 4) | |
Holbein Artists’ Oil Colors | ||
Ceramic White | Strontium titanate | Poppyseed oil |
Foundation Color | Lead white (PW 1) | Linseed oil |
Neo-Quick Base | Titanium dioxide (PW 6) | Linseed oil, alkyd resin, and petroleum solvent |
Neo-Zinc White | Zinc oxide (PW 4) | Poppyseed and safflower oils |
Permanent White | Titanium dioxide (PW 6) | Poppyseed and safflower oils |
Quick Drying White | Titanium dioxide (PW 6), calcium carbonate (PW 18) | Poppyseed oil and alkyd resin |
Silver White | Lead white (PW 1) | Linseed oil |
Titanium White | Titanium dioxide (PW 6) | Poppyseed oil |
Lefranc & Bourgeois Artists’ Oil Colors | ||
Flake White Hue | Titanium dioxide (PW 6), zinc oxide (PW 4) | Safflower oil |
Silver White | Lead white (PW 1) | Safflower oil |
Titanium White | Titanium dioxide (PW 6), zinc oxide (PW 4) | Safflower oil |
Titanium-Zinc White | Titanium dioxide (PW 6), zinc oxide (PW 4) | Safflower oil |
Zinc White | Zinc oxide (PW 4) | Safflower oil |
Maimeri Puro Oil Colors | ||
Titanium White | Titanium dioxide (PW 6) | Poppyseed and safflower oils |
Zinc White | Zinc oxide (PW 4) | Poppyseed and safflower oils |
Michael Harding’s Artist Oil Colors | ||
Cremnitz White | Lead white (PW 1) | Linseed oil |
Cremnitz White | Lead white (PW 1) | Walnut oil |
Flake White | Lead white (PW 1), zinc oxide (PW 4) | Walnut oil |
Flake White No. 1 | Lead white (PW 1), zinc oxide (PW 4) | Poppyseed oil |
Foundation White | Lead white (PW 1) 50%, titanium dioxide (PW 6) 50% | Acid-refined linseed oil |
Titanium White | Titanium dioxide (PW 6) | Safflower oil |
Titanium White No. 1 | Titanium dioxide (PW 6) | Poppyseed oil |
Titanium White No. 2 | Titanium dioxide (PW 6), zinc oxide (PW 4) 25% | Acid-refined linseed oil |
Zinc White | Zinc oxide (PW 4) | |
Natural Pigments Rublev Colours Artists Oils | ||
Flemish White | Lead sulfate (PW 2), lead white (PW 1) | Alkali-refined linseed oil |
Lead White No. 1 | Lead white (PW 1) | Alkali-refined linseed oil |
Lead White No. 2 | Lead white (PW 1) | Walnut oil |
Ceruse |
Lead white (PW 1), calcium carbonate (PW 18) | Alkali-refined linseed oil |
Venetian White | Lead white (PW 1), barium sulfate (baryte, PW 22) | Walnut oil and alkali-refined linseed oil |
Crystal White | Lead white (PW 1), leaded crystal glass | Walnut oil and alkali-refined linseed oil |
Mica-Lead White | Lead white (PW 1), mica (PW 20) | Walnut oil and alkali-refined linseed oil |
Old Holland Classic Oil Colors | ||
Cremnitz White | Lead white (PW 1) | Cold-pressed linseed oil |
Flake White No. 1 | Lead white (PW 1), zinc oxide (PW 4) | Cold-pressed linseed oil |
Mixed White No. 2 | Titanium dioxide (PW 6), zinc oxide (PW 4) | Cold-pressed linseed oil |
Titanium White | Titanium dioxide (PW 6), zinc oxide (PW 4) | Cold-pressed linseed oil |
Zinc White | Zinc oxide (PW 4) | Cold-pressed linseed oil |
Pēbēo Fragonard Couleurs Extra-Fines Oil Colors | ||
Titanium White | Titanium dioxide (PW 6) | |
Zinc and Titanium White | Titanium dioxide (PW 6), zinc oxide (PW 4) | |
Zinc White | Zinc oxide (PW 4) | |
Royal Talens Rembrandt Oil Colors | ||
Mixed White | Titanium dioxide (PW 6), zinc oxide (PW 4) | |
Titanium White | Titanium dioxide (PW 6), zinc oxide (PW 4) | Linseed oil |
Titanium White | Titanium dioxide (PW 6), zinc oxide (PW 4) | Safflower oil |
Transparent White | Titanium dioxide (PW 6), zinc oxide (PW 4) | |
Zinc White | Zinc oxide (PW 4) | Linseed oil |
Zinc White | Zinc oxide (PW 4) | Safflower oil |
Vasari Classic Artists’ Oil Colors | ||
Flake White | Lead white (PW 1) | Linseed oil |
Titanium White | Titanium dioxide (PW 6), zinc oxide (PW 4) | Linseed oil |
Titanium-Zinc White | Titanium dioxide (PW 6), zinc oxide (PW 4) | Linseed oil |
Zinc White | Zinc oxide (PW 4) | Linseed oil |
Martin/F. Weber Professional Permalba® Oil Colors | ||
Permalba White (original) | Titanium dioxide (PW 6), zinc oxide (PW 4) | Alkali-refined safflower oil |
Titanium White | Titanium dioxide (PW 6) | |
Zinc White | Zinc oxide (PW 4) | |
Williamsburg Handmade Artists’ Oil Colors | ||
Flake White | Lead white (PW 1) | Alkali-refined linseed oil |
Silver White | Lead white (PW 1), zinc oxide (PW 4) | Alkali-refined linseed oil |
Titanium White | Titanium dioxide (PW 6) | Alkali-refined linseed oil |
Titanium-Zinc White | Titanium dioxide (PW 6), zinc oxide (PW 4) | Alkali-refined linseed oil |
Zinc White | Zinc oxide (PW 4) | Alkali-refined linseed oil |
Winsor & Newton Artists’ Oil Colors | ||
Cremnitz White | Lead white (PW 1) | |
Flake White No. 1 | Zinc oxide (PW 4), lead white (PW 1) | Safflower oil |
Flake White No. 2 | Lead white (PW 1), zinc oxide (PW 4) | Safflower oil |
Flake White Hue | Titanium dioxide (PW 6) | |
Foundation White | Lead white (PW 1), zinc oxide (PW 4) | Linseed oil |
Titanium White | Titanium dioxide (PW 6), zinc oxide (PW 4)** | |
Transparent White | Titanium dioxide (PW 6) | |
Underpainting White | Titanium dioxide (PW 6), zinc oxide (PW 4) | |
Zinc White | Zinc oxide (PW 4) |
Table Notes
* Only pigments identified on the manufacturer’s labels or literature are listed in the table. The absence of zinc oxide in the list does not mean zinc white is not included in the paint unless the manufacturer complies with standard ASTM D 4302 and lists all pigments used. However, zinc oxide can be used in minimal amounts as an additive, typically less than 2%, and not be identified on the label in compliance with ASTM D 4302.
** The manufacturer notes a “small amount of zinc white” is added.
The table was prepared in June 2007, with additions in 2014. Some of the information in the table may have changed. For an updated table of the current pigments of commercial oil colors, please see Appendix A. The revised and updated table in Appendix A clearly shows how some manufacturers have reduced or eliminated zinc oxide in their white formulations.
The table identifies the pervasiveness of zinc in artists’ oil paints not only labeled “zinc white,” but also in paints labeled “flake white” (basic lead carbonate) and “titanium white” (titanium dioxide). The prevalence of zinc in paintings may present problems shortly. Mark Gottsegen, the author of The Painter’s Handbook, wrote, “We think artists who use oil paints, and thus any white oil paint, are going to have problems with their paintings. Maybe not today or next week, or even next year, but within ten years, certainly.” [6]
Physical Properties of Zinc White
Fig. 3 Transmission electron microscopic (TEM) image showing typical zinc oxide particles.
Let’s examine its properties and history to help us understand why zinc white is so commonly found in white oil paint today. Zinc oxide is a fine white powder that absorbs ultraviolet light at wavelengths below 366 nm. The zinc oxide particles may be granular or nodular (0.1–5 µm) or acicular (needle-shaped, 0.5–10 µm). Particles produced by the wet process have an amorphous character (sponge form, particles up to 50 µm).[7]
A unique property of zinc oxide is that it is excitonic; it absorbs ultraviolet radiation and becomes defective, molecularly speaking.[8] Ultraviolet radiation causes aging in most things on earth, including human skin. Zinc oxide is used in many coatings, whereby absorbing ultraviolet radiation can extend the life of the coating.
Many standard specifications have been established for the more important uses of zinc oxide. Typical classifications include indirect (French) process, direct (American ) process, wet process, pharmaceutical grade, chemically pure grade, etc. Manufacturers have their standards, too. The chemically pure grade made by the indirect process contains over 99% zinc oxide.
Formerly, zinc white was sold in various qualities and degrees of whiteness. “White seal” and “green seal” zinc white contain over 99% zinc oxide. “Red seal” and “gold seal” grades were slightly less pure, and “gray seal” zinc white contains metallic zinc.[9] The terms gold seal, silver seal, red seal, green seal, and white seal are still common in Europe.
The most common grade of zinc oxide used in artists’ oil paint is the indirect process, chemical pure grade. In Europe, it is designated as either a white or green seal. Table 2 shows the typical physical specifications for the French process, green seal zinc oxide.
Table 2 Typical Properties of Zinc Oxide Pigment (French Process)
Zinc Oxide Purity |
99.5% |
Mean Particle Size | 0.33 μm |
Particle Surface Area |
3.2 m2/g |
Passing Through 325 Mesh |
99.99% |
Oil Absorption |
12 lbs oil for 100 lbs zinc oxide |
Refractive Index |
1.95–2.1 |
Crystal Structure |
Hexagonal |
MOHS Hardness | 4–4.5 |
Density | 5.65–5.68 g/cm3 |
Apparent Density | 40 lb/ft3 |
Bulk Density |
1 lb = 0.0214 gallon |
Pounds Per Solid Gallon | 46.7 lbs |
Brief History of Zinc White
Zinc has long been known as a byproduct of copper smelting. The Romans called it “cadmia” and used it in the production of brass. In the mid-18th century, the German chemist Cramer discovered that cadmia could be obtained by the combustion of metallic zinc. Courtois de Dijon began to produce zinc white in 1781 in France. In 1782, zinc oxide was suggested as a white pigment. That year, Guyton de Morveau at L’Académie de Dijon, France, reported on white pigments and the raw materials that might serve as white pigments, including zinc oxide. He suggested zinc oxide as a substitute for lead white.[10]
It took about 50 years before artists adopted zinc white. As early as 1834, according to Church, a dense form of zinc white was introduced by the firm Winsor & Newton under the name “Chinese white.” [11] The major obstacle in its use among artists was its poor drying qualities in linseed oil. In 1835-1844, Leclaire in France showed that this difficulty could be overcome by using zinc oxide in oil that had been made faster drying. By 1850, it was regularly made as an oil paint.
In 1845, Leclaire began industrial zinc oxide production in Paris with the indirect or French process. Around 1850, S. Wetherill of the New Jersey Zinc Company perfected a furnace in which the zinc was reduced by the partial combustion of coal and reoxidized at the furnace exit (direct or American process). This process was later improved but is no longer used in Europe and America but is still used in China. A third industrial production process exists, but this wet process is less widely used.[12]
The only significant white pigment was lead white until that time. Zinc oxide began to replace lead white in many types of paint because it had the advantages of being nontoxic, not darkening in the presence of sulfurous gases, and offering a brilliant white. Lead white had served the old masters well, but changes in color preferences during the 19th century created the demand for more brilliant colors. Artists found that zinc oxide was not as opaque as lead white was and provided cool, brilliant whites in oil paint. The transparency of zinc white makes it valuable for making tints with other colors. Tints made with transparent whites show the nuances of a color’s undertone to a greater degree than tints made with more opaque whites.
Early Problems with Zinc White
Despite its many advantages, it was soon found that zinc white oil color also has a drawback; it makes a somewhat brittle oil paint film. Zinc whites’ brittleness can cause cracks in paintings after only a few years if used by itself or in excess. During the latter half of the 19th century, some artists used zinc white as a ground for their oil paintings. They wanted the brilliant white to obtain highly saturated colors in their works but did not realize its long-term disadvantage. After years, many paintings developed cracks, whereas older works painted on traditional grounds remained free from cracks.[13]
The effects of zinc oxide in paint have been investigated since the early 20th century. For example, it was found that zinc oxide shows appreciable reactivity in drying oils.[14] Zinc oxide tends to saponify the fatty acid component of certain oils, with the degree of soap formation dependent upon the particle size of the pigment, with the finest particles resulting in more rapid soap formation.[15] The formation of soaps is beneficial in some vehicles and is one reason zinc white has long been used as an additive in titanium white paints. However, this reactivity can be a two-edged sword. Researchers also found it can rapidly form a hard and sometimes brittle film, especially when using zinc oxide as a pigment.[16]
In paints and coatings, zinc oxide is no longer the principal white pigment, although artists use its superb white color as noted above. It is used as an additive in exterior paints for wood preservation, antifouling, and anticorrosion paints.[17] It improves film formation in some paint vehicles and resistance to mildew (having a synergistic effect with other fungicides) because it reacts with acidic oxidation products and can absorb ultraviolet radiation.
Still Used by Artists Today
If problems were observed since the early part of the 20th century, why is zinc white still used in artists’ oil paints today? The problems mentioned above were primarily observed when zinc white was used alone or in excessive amounts, especially in the ground layers of paintings. The cracking and embrittlement of dried paint films could be minimized or eliminated when zinc white was mixed with other white pigments or used sparingly. In addition, its brilliant white color is seductive to artists; hence manufacturers continue to supply the demand for paint with zinc white. Manufacturers add zinc white to artists’ white colors to offset the shortcomings of other pigments.
In the first half of the 20th century, a new white pigment appeared on the scene—titanium dioxide. This pigment was more opaque, less reactive than zinc white, and did not form brittle oil paint film. Titanium white by itself, however, has too much tinting strength for some use in artists’ colors and makes stringy oil paint.[18] Manufacturers often combine titanium white with zinc oxide to produce a manageable white paint.
Shortly after the introduction of titanium white, reports appeared to confirm the advantages of zinc white in oil colors. White oil paint containing as little as 10 to 15% zinc oxide yellowed less, especially when ground in safflower oil.[19] Henry Levison favorably reports on white paint containing zinc oxide in his book, Artists’ Pigments, Lightfastness Tests and Ratings. Among the different white colors he studied, paint film composed of safflower oil and 15 to 20% zinc white to titanium white withstood his test. Levisons’ tests involved exposure to the sun for several months.[20] The study by the Smithsonian scientists was done over 28 years.
There is no question of the advantages to the visual appearance of white oil paint incorporating zinc oxide, especially titanium white. This is why zinc oxide is commonly used in titanium white oil colors. The combination of titanium white and zinc white yellows less than other combinations of white pigments in oil. However, artists may be giving up the long-term integrity of the paint film for a short-term advantage of less yellowing, which Levison found is reversible in white oil paints.[21]
Other Potential Problems
If these problems were not enough, other problems began to surface. Earlier, we learned that zinc is very reactive to specific fatty acids in the oil. For example, zinc oxide reacts with stearic acid to form metallic soaps containing zinc alkonate and zinc stearate. Soap formation occurs when zinc oxide is used in an oil medium with a high proportion of acid groups. These substances can cause efflorescence on the surface of the paint film, often producing hazy white patches on the surface of a painting.[22] Because zinc is a divalent metal, oil tends to cross-link, causing the paint to excessively thicken or increase viscosity upon storage.[23]
An advantage is the strong ultraviolet absorbency of zinc oxide, which protects lead and titanium pigments from photochemical changes. On the other hand, researchers have shown that near-ultraviolet light can promote the formation of hydrogen peroxide, a process that causes the dehydration of other pigments and subsequent embrittlement.[24]
Should Artists Stop Using Zinc White in Oil Paint?
Should artists toss out their tubes of white oil color containing zinc white? If artists are concerned about the long-term prospects of their paintings, the answer is affirmative. Does this mean that zinc white should be removed from the list of pigments suitable for serious artistic use? Maybe. For the time being, it should only be used in the paint where the objective is not permanent.
Mecklenburg and Tumosa did not examine every grade of zinc oxide. Presumably, the grade of zinc oxide in the paint studied was of the French or indirect process since this is the type most widely used in artists’ oil paints. Generally, commercial zinc white particles have nodular or irregular shapes in sizes ranging from 0.1 microns to slightly greater than one micron. It is known that grades of zinc oxide with acicular particle shapes have greater covering ability or hiding strength, and this shape may alter its reactivity in oil. However, according to Robinson, acicular zinc oxide is more reactive in paint vehicles and not less.[25] In addition, the acicular form of zinc oxide is costly and primarily used in specialty polymers, not paint.[26] Whereas larger particle-size zinc oxide is less reactive, the larger size makes it unsuitable for paint.
The initial condition of zinc white powder is essential, especially the water content, before mixing with drying oils and other additives. Zinc oxide is known to be hygroscopic, meaning it absorbs water when exposed to air and becomes sticky—the particles of zinc white stick to one another. If “sticky” zinc oxide is used to make oil colors, some moisture can be trapped inside the paint, which may lead to cracking and peeling. To avoid this problem, paint manufacturers must heat (above 600° C.) the sticky zinc oxide to remove the water content. However, this is typically not done by artists’ color manufacturers.
According to Mahmud, the hygroscopic property of zinc oxide causes it to react with the atmosphere after prolonged exposure to moisture and sunlight. Zinc oxide can absorb moisture from the air, causing physical expansion of the paint film; similarly, it can lose moisture if the air is dry, triggering contraction. This results in the paint film’s physical stress, which can lead to cracking.[27]
On a more positive note, it may be possible to mitigate the reactivity of zinc oxide in oil and reduce its effects of cracking and peeling. Titanium white is reactive to light and certain substances in paint. Pigment manufacturers coat titanium dioxide particles with silica and alumina to reduce this photochemical reactivity. Several patents exist for coating or doping zinc oxide particles, such as that used for thermal coatings.[28] It may be possible to coat zinc oxide particles, such as the coating of titanium dioxide, to produce zinc white pigment that does not cause cracking and peeling in oil paint.
Conclusion
Paints made with zinc oxide and drying oils become extremely brittle in as little as three years. Paints containing zinc oxide exhibit severe delaminating problems after drying, especially zinc oxide paint on acrylic emulsion grounds. Even commercial lead white and titanium white oil paints containing zinc oxide become quite brittle after seven years of drying.
Of course, not every painting containing zinc white will crack, and its paint will fall off the support. Artists of the Pre-Raphaelite Brotherhood (19th century) often used zinc white in their paintings. One such painting, Ophelia (1851–52) by Sir John Everett Millais, has areas of zinc white priming.[29] Remarkably, the painting is in generally good condition and does not show problems due to the reserves of zinc white.[30] However, it is impossible to draw a parallel between the present condition of 19th-century paintings to the future state of paintings made by today’s artists. First, the materials used then are significantly different from those used today. Second, individual painting techniques may moderate the problems caused by the materials. Third, oil paintings are complex structures with many chemical and physical interactions that cannot always be predicted or explained with current scientific methods.
Fig. 4 Ophelia (1851–52) by Sir John Everett Millais has areas of zinc white priming.
Mecklenburg and Tumosa’s paper forewarns us about the potential problems with oil paints containing zinc white commonly used by artists today. Artists may ignore the report and continue using zinc in their paintings—perhaps at their peril. Whatever the choice, the paper helps artists better understand the materials used in their work.
Notes and Sources
1. Marion F. Mecklenburg and Charles S. Tumosa (2007). “The chemical and mechanical effects of pigments on drying oils.” Unpublished. pp. 13–14.
4. Marion Mecklenburg, private communication.
5. ASTM D 4302 Standard Specification for Artists’ Oil, Resin-Oil, and Alkyd Paints, see section 5.1.7: “Mixed Pigments—Artists’ paints containing more than one pigment comply with this specification if all colored pigments included in the mixture are on the suitable pigment list (Table 1) and provided the mixture itself has passed all other test requirements in this specification. The Common Names for the pigments in the mixture, or the word ‘Mixture,’ must appear under the title in letters no less than the next type size smaller than the title. …If the word ‘Mixture’ is used under the title, the Common Names of the pigments in the mixture, as given in Table 1, must be listed along with their Colour Index Names and the Lightfastness Category of the mixture somewhere on the label.” ASTM does not enforce its voluntary standards. Some companies may copy ASTM terminology without actually conforming with ASTM D 4302.
6. Mark D. Gottsegen (2007). “Zinc oxide and its effects on drying oil.” Discussion Forum. AMIEN: Art Materials Information and Education Network. http://www.amien.org/forums/showthread.php?t=366. (This link is inactive.)
7. Gerhard Auer, Wolf-Dieter Griebler, Burkhardt Jahn. (2005) “White Pigments.” Industrial Inorganic Pigments. 3rd Edition. p. 90.
8. For the definition of “excitonic,” see the Wikipedia article “Exciton.” Wikipedia. http://en.wikipedia.org/wiki/Exciton
9. Rutherford J. Gettens, George L. Stout (1966). Painting materials: A short encyclopedia. New York: Dover Publications. p. 177.
10. D. B. Faloon (1925). Zinc oxide history, manufacture, and properties as a pigment. New York.
11. A. H. Church. The chemistry of paints and painting. 3rd ed. London: Seely, Service, and Company. p. 134.
12. Gerhard Auer (2005), pp. 89–90.
13. Michael Douma, ed. (2001). “Zinc white—history” WebExhibits. http://webexhibits.org/pigments/indi...zincwhite.html
14 L. A. O. O’Neill, R. A. Brett (1969) “Chemical reactions in paint films.” Journal Oil Chemical Assoc. 52 (11) (1969) pp. 1054–1074.
15. S. H. Bell (1970). “Controlling zinc oxide hazing in gloss paints.” Paint and varnish production, Vol. 60 No. 4. pp. 55–60. See also Payne, H. F. (1961). Organic coating technology. New York: John Wiley & Sons.
16. A. E. Jacobsen (1941) “Zinc soaps in paints.” Ind. Engin. Industry 33 (10) (1941) pp. 1254–1256.
17. G. Meyer (1986). New application for zinc. New York: Zinc Institute Inc.
18. Henry W. Levison (1976). Artists’ pigments, lightfastness tests, and ratings. Hallandale, Florida: Colorlab. p. 30.
19. Henry W. Levison (1985). “Yellowing and bleaching of paint films.” Journal of the American Institute of Conservation, 1985, Volume 24, Number 2, Article 2. pp. 69–76. See also Levison (1976). Artists’ pigments, lightfastness tests, and ratings. p. 31
20. Levison (1976). pp. 32–34.
22. Eugena Ordonez, John Twilley (1988). “Clarifying the haze, efflorescence on works of art.” Western Association for Art Conservation (WAAC) Newsletter. January 1998 Volume 20 Number 1.
23. G. P. A. Turner (1988). Introduction to paint chemistry and principles of paint technology. London: Chapman & Hall. p. 252.
24. Nicholas Eastaugh (2004). Pigment Compendium: A dictionary of historical pigments. Elsevier. P. 407. See also John S. Mills, Raymond White (1994). The organic chemistry of museum objects. Elsevier p. 165.
25. Peter John Robinson, private communication. Dr. Robinson has been a consultant to the zinc industry for the past 40 years.
26. Shahrom Mahmud, private communication. Mr. Mahmud is a reviewer for the Elsevier journal Materials Science Engineering, the author of 11 papers on zinc oxide manufacturing and 20 publications, and a consultant to zinc oxide factories in several countries.
27. Shahrom Mahmud, private communication.
28. United States Patent 4331706, Composite zinc oxide coating on an inert pigment core product and process; United States Patent 5589274, Thermal control coating; United States Patent 5770269, Thermal control coating; United States Patent 7235298, Doped zinc oxide powder, the process for its preparation, and its use.
29. Joyce H. Townsend, Jacqueline Ridge, and Stephen Hackney (2004) Pre-Raphaelite painting techniques. London: Tate Publishing. p. 137.
30. Leslie Carlyle, private communication.
Is it possible to achieve the transparency of Titanium white paint with the addition of Safflower oil? And what is the difference between Safflower oil and refined linsed oil? Questions..questions..and more questions.
George, thank you very much.
Permalba white has been a staple of many artists (and I know many an instructor that swears by it, it's in countless instructors materials lists. You'd think we'd see an endemic of cracking in contemporary paintings. I know there are numerous examples of cracking, but usually can be explained by not following best painting practices. If the problem was as serious as the study seems to indicate, I'd think the problem would happen much more regularly. Just use lead white, right? :)
Anyway, I guess my point is just, this warrants further study. I appreciate the points you raised in the closing paragraph.